La prefabrication, procede novateur pour la construction rapide de Bioscience
La KU Leuven et l'Institut flamand de biotechnologie (VIB) mettront en service un nouveau bio-incubateur sur le campus Arenberg III de Louvain en 2024. C’est déjà le cinquième modèle du genre. L'imposante tour abritera 3.300 m² de laboratoires et de bureaux flexibles. Sa construction s'est déroulée en l’espace record de deux ans grâce à une préfabrication poussée de la structure portante et à l’exécution aussi simultanée que possible des différentes tâches de finition.
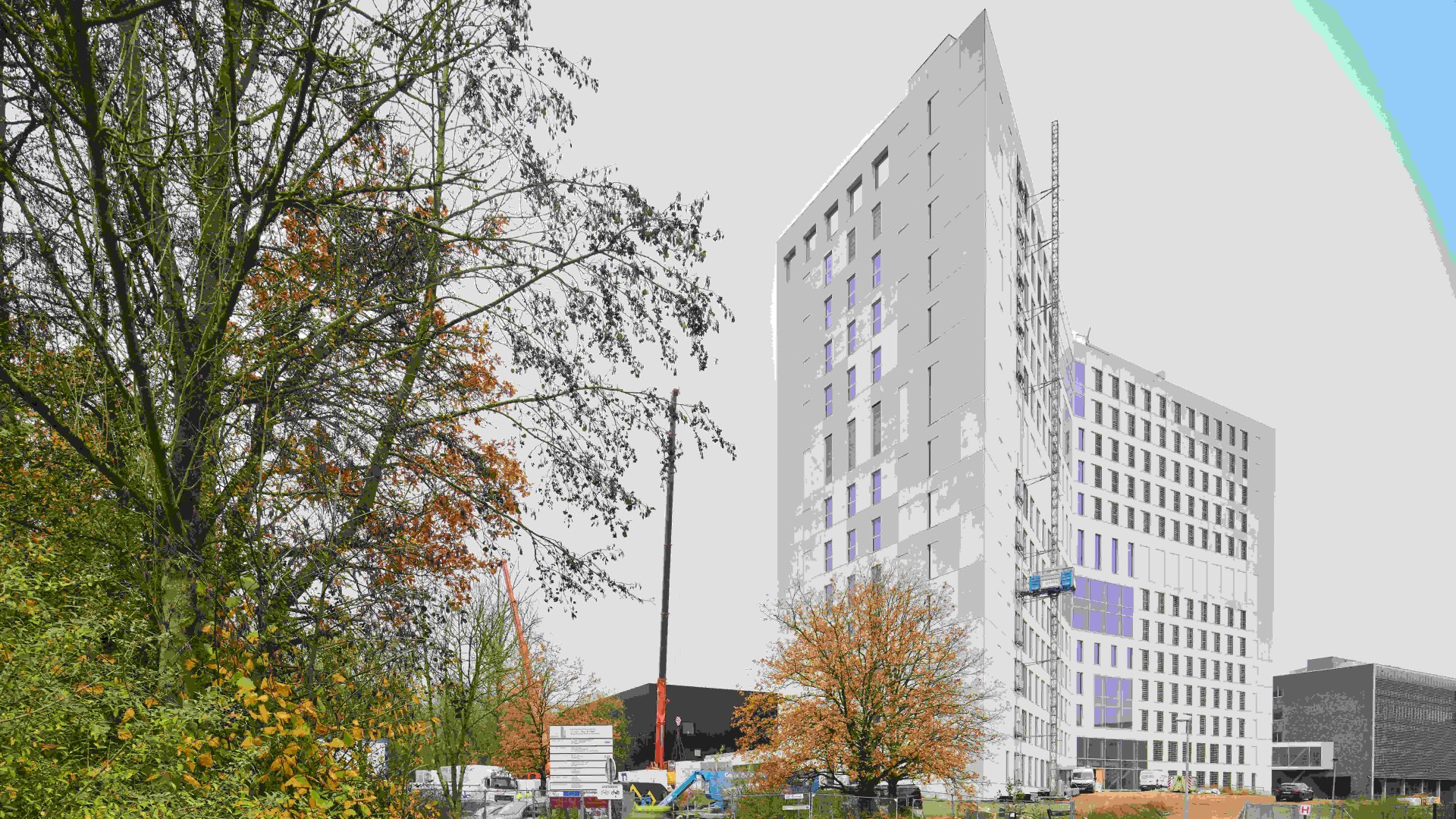
Bioscience : c'est ainsi que les initiateurs – la KU Leuven et l'Institut flamand de biotechnologie – ont baptisé le nouveau bio-incubateur qui ambitionne d’accueillir les quelque 160 employés de start-ups et d’entreprises biotechnologiques de renom qui s'y installeront. Le programme de construction intensif mis en œuvre sur cette modeste parcelle de terrain à bâtir a débouché sur une tour de 13 niveaux hors sol et cave. À l’instar d’autres édifices aux allures grandioses, comme la tour Imec, le château d'Arenberg ou encore le bâtiment en hauteur prévu dans le plan directeur du parc scientifique d'Arenberg, Bioscience a le potentiel de devenir une véritable référence pour le campus. Comme sur les bâtiments voisins « Quadrivium » et « Leuven Chem & Tech », le volume de la poutre tient lieu de nouvelle place publique. Le pli caractéristique de la façade crée une place logistique abritée sur la face nord à faible circulation.
« À l'intérieur, la poutre pliée offre l'avantage de rendre les différents flux naturels et intuitifs. Les utilisateurs accèdent à l'entrée principale située au +1 par un paysage naturellement ascendant. Les nombreux cyclistes restent au niveau de la rue tandis que la logistique quotidienne est assurée grâce à la nouvelle connexion avec Leuven Chem & Tech. Le bio-incubateur opère lui aussi une séparation claire entre les flux de marchandises et de personnes », explique Wim De Greef, chef de projet senior de l’entreprise générale CIT Blaton.
Un concept flexible
En plus de satisfaire à des critères urbanistiques et logistiques, la poutre pliée offre une réponse logique à l'orientation du terrain. « Le coude maximise l’exposition au soleil de la façade nord et réduit celle de la façade sud. Parallèlement, les façades est et ouest, difficiles à contrôler du point de vue climatique, sont réduites au minimum. Ou comment créer un climat intérieur agréable en appliquant des solutions simples », se réjouit Wim De Greef.
La ventilation est la principale installation présente dans un laboratoire. Le principe mis en œuvre pour Bioscience se base sur un système global pour tous les laboratoires du bâtiment et un système distinct pour les zones générales situées au bas du bâtiment. « Les étages abritant les laboratoires généraux ne sont pas techniquement divisés en différentes zones, étages ou autres. Ils sont desservis par un seul système qui fournit de l'air à tous les étages. Les unités de traitement de l'air distribuent l'air à travers un système de canaux commun selon le concept de l'anneau. La production d'énergie dans le bâtiment ne fait appel à aucune énergie fossile.
Le bâtiment a été doté d'une seule grille universelle capable d’intégrer toutes les fonctions. « Le programme presque complet peut être installé quasiment à n'importe quel endroit du bâtiment, ce qui permettra au bio-incubateur de répondre dans le futur à une question de recherche inconnue. Parallèlement, les décisions relatives à l'agencement final ont pu être reportées assez longtemps durant la phase de construction, ce qui a permis aux locataires de bénéficier d'une certaine flexibilité », poursuit Wim De Greef.
Optimalisation du planning
Le calendrier constituait l'un des principaux défis de CIT Blaton. L'enveloppe étanche au vent et à l'eau du nouveau bio-incubateur devait être livrée début 2024. « Ce n'était pas gagné, car lors de la phase de démarrage à la mi-2021, nous étions encore en pleine pandémie de Covid avec son cortège de mesures sanitaires. Pour pouvoir construire en s'affranchissant au maximum de ces restrictions et des conditions météorologiques, nous avons proposé de préfabriquer entièrement les murs et les poutres », explique Wim De Greef. « Nous avons réalisé l'étude entièrement en interne par l'intermédiaire de notre département de préfabrication. »
Non contente de préfabriquer la structure portante, l'équipe de Wim De Greef a sorti quelques autres mesures de son sac à malices pour réduire au maximum le délai d'exécution. « Nous avons par exemple commencé à placer les éléments de façade en béton architectonique avant même l'achèvement de la structure portante. Ce qui a entraîné l’exécution simultanée d’une multitude d'activités : pose des éléments préfabriqués en béton aux étages supérieurs, installation des fenêtres et murs-rideaux, travaux d’étanchéité, installation des panneaux d'isolation, travaux de jointoiement, etc. En interne aussi, nous avons veillé à ce que les sous-traitants entament leurs travaux techniques le plus rapidement possible. L'orchestration de ces différentes activités a nécessité une coordination minutieuse entre les différents sous-traitants et fournisseurs », confie Wim De Greef.
Sous la supervision d’un géomètre
Pour s’assurer que l'organisation du chantier suive le rythme élevé des activités de construction, l'entrepreneur a déployé deux grues de construction. « Nous avons soigneusement planifié le travail de chaque grue et l’avons évalué et corrigé le cas échéant au jour le jour. La livraison et l'installation des éléments de façade en béton architectonique constituaient également un défi. Les éléments ont été livrés just in time sur le site depuis les Pays-Bas et montés directement sur la façade. Tous les points d'ancrage avaient été appliqués préalablement sur la façade. La position correcte de ces éléments a été contrôlée en détail par un géomètre. En effet, un seul point d'ancrage mal positionné aurait entraîné l'immobilisation des grues, des transports et de la main-d'œuvre. Nous avons par ailleurs pris des dispositions claires avec le transporteur des éléments de façade. Chaque jour, deux camions faisaient la navette entre les Pays-Bas et le site du campus Arenberg. »
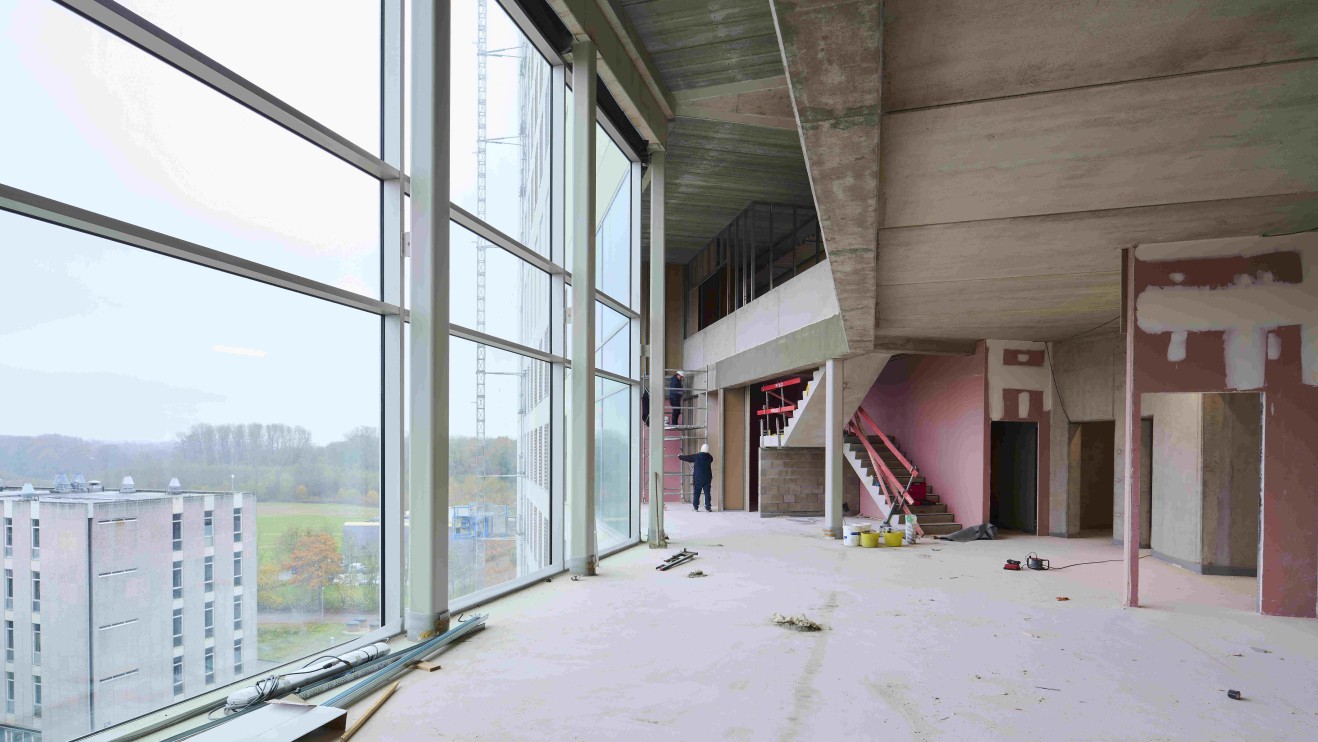
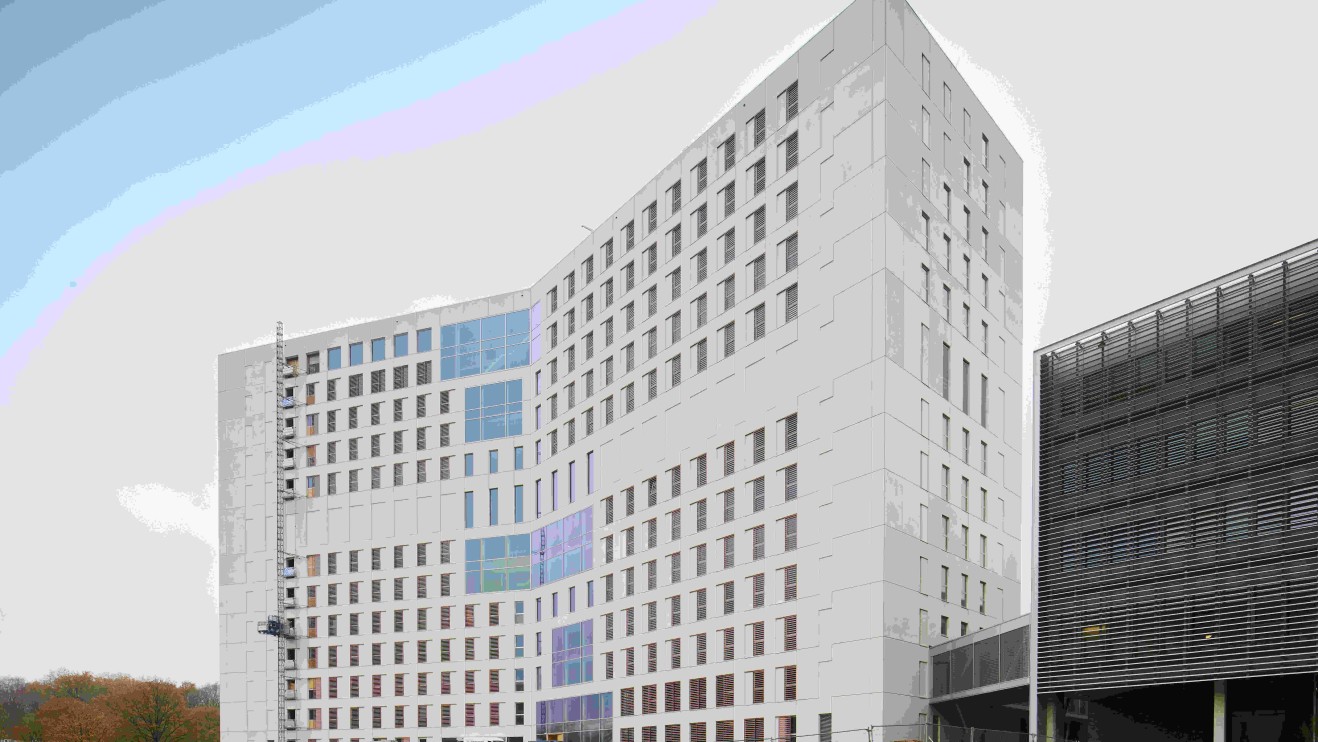