Smart Slab: une toiture en béton ultra fine, légère et incurvée
Des chercheurs de l’Ecole polytechnique fédérale de Zurich ont mis au point une toiture en béton qui rassemble plusieurs particularités innovantes. Entièrement réalisée à l’aide de méthodes de planification et de fabrication digitales, elle est à la fois ultra fine, légère et courbée. Ses concepteurs ont ainsi réussi à allier la résistance structurelle du béton à la liberté de conception de l’impression 3D.
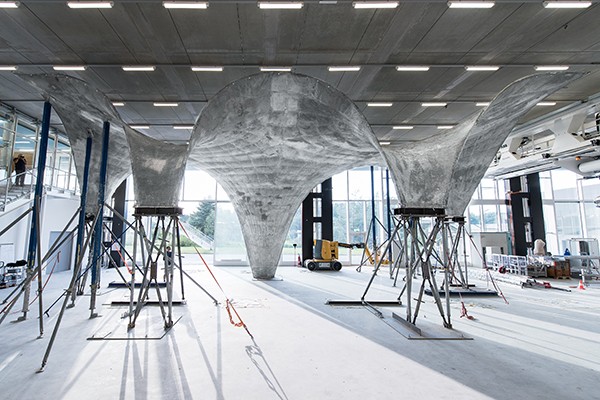
Curiosité, objet architectural, prouesse technique: la toiture «Smart Slab» est tout cela à la fois. Développée par le groupe de recherche de Benjamin Dillenburger (professeur assistant en technologies du bâtiment numérique à l'ETH de Zurich), elle combine les particularités d’être légère et incurvée, tout en étant faite de béton. Ses 80 m2 sont composés de onze segments du matériau et pèsent 15 tonnes, soit environ deux fois moins qu’une toiture traditionnelle en béton. A ses endroits les plus fins, la structure ne dépasse pas les 20 mm d’épaisseur.
Avant la vraie version, les chercheurs ont réalisé un prototype sur une structure de câbles en acier. (© Block Research Group, ETH Zurich / Naida Iljazovic)
Il a fallu plus de quatre ans aux scientifiques pour produire cette toiture hors normes, notamment parce qu’ils souhaitaient intégrer plusieurs partenaires au projet. Avant la réalisation finale de l’ouvrage, un prototype a d’abord été conçu à l’aide d’une structure d’échafaudage réutilisable et d’un réseau de câbles en acier tendus, sur lesquels un textile en polymère servait de coffrage pour le béton. Ce choix a permis aux chercheurs d’économiser des matériaux, mais aussi d’expérimenter des formes et des types de conceptions nouveaux.
Lors de la fabrication du prototype, un textile en polymère faisait office de coffrage pour le béton. (© Block Research Group, ETH Zurich / Naida Iljazovic)
Coffrage en sable et bois
Au moment de réaliser la vraie toiture quelques mois plus tard, les scientifiques ont eu recours à l’impression 3D. Ils l’ont utilisée non pas pour le toit en lui-même, mais pour le moule qui a servi à le construire. Le coffrage de la toiture a été divisé en sections de la taille d’une palette pour faciliter à la fois l’impression et le transport, et a été produit par deux sociétés partenaires. L’une a réalisé une partie du moule en impression 3D de sable et l’autre a fabriqué une portion en bois à l’aide d’une machine-outil à commande numérique (Cnc). Cette partie en bois du coffrage donne forme à l’élément supérieur de la dalle-toiture. Elle a aussi permis de laisser des zones creuses dans la structure, lesquelles réduisent l’utilisation de matériaux et le poids tout en créant de l’espace pour les câbles électriques et autres éléments techniques qui s’intègrent directement dans la Smart Slab.
Il a fallu trouver le bon mélange de béton pour pouvoir le pulvériser et le faire tenir dans les éléments verticaux de la toiture. (© Block Research Group, ETH Zurich / Naida Iljazovic)
Après leur fabrication, les différents morceaux du moule ont permis de procéder à la réalisation de la toiture en elle-même. Dans un premier temps, les professionnels collaborant au projet se sont chargés de pulvériser du béton fibré sur le coffrage en sable afin de constituer la surface finement nervurée de la coque inférieure. Les nervures principales de la toiture ont pour vocation de supporter les charges, alors que les plus petites, en filigrane, assurent surtout des fonctions acoustiques et architecturales. Après la coque inférieure recouverte de matériaux, les ouvriers ont coulé le béton restant dans le coffrage en bois.
Ces différentes étapes ont nécessité la mise au point d’une méthode de pulvérisation spécifique et surtout, d’un mélange de béton assez fluide pour être pulvérisé, mais en même temps suffisamment visqueux et consistant pour ne pas s’écouler du coffrage, y compris dans les endroits verticaux.
La toiture en béton de 80 m2 pèse seulement 15 tonnes. (© Block Research Group, ETH Zurich / Michael Lyrenmann)
Une fois le béton coulé, il a fallu respecter un processus de durcissement de deux semaines en atelier avant que les différents segments de la toiture puissent être transportés et assemblés sur site.
Voir la Chronique n°42 du 19/10/18 pour la suite de l’article.