Le béton s’ancre dans la durabilité
Depuis le début du XXe siècle, la croissance démographique a entraîné des constructions massives et à grande échelle de logements, infrastructures, ouvrages d’art et autres réalisations. Dire que, sous nos latitudes, le béton se pose en choix incontournable revient à enfoncer des portes ouvertes. La production de ce matériau pose néanmoins de solides questions environnementales, en particulier, pour son composant le plus énergivore: le ciment. C’est pourquoi le secteur s’active pour réduire son empreinte carbone. Entre autres.
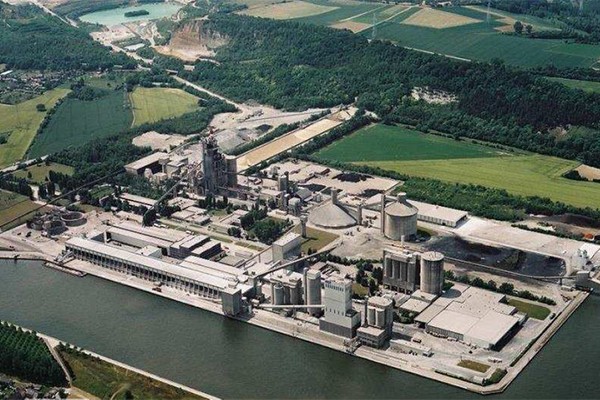
Le secteur cimentier n’a donc pas attendu le déferlement de la vague verte pour se préoccuper de ses émissions de CO2 et de ses autres composantes énergivores. Il s’agissait d’innover, pour des raisons environnementales et économiques. En 2016, l’industrie cimentière a ainsi franchi un pas supplémentaire vers l’efficacité énergétique et la réduction des émissions de CO2, avec une Roadmap à l’horizon 2050 dans le cadre des accords de branche de deuxième génération avec la Wallonie. Cette Roadmap couvre trois leviers: l’utilisation rationnelle des rerssource, l’amélioration de l’efficacité énergétique et la capture, le stockage et l’utilisation du CO2.
Une partie du site où sont stockés les combustibles de substitution.
Utilisation rationnelle des ressources
Les spécificités du procédé de fabrication du ciment ainsi que le caractère non renouvelable des ressources primaires - tel le calcaire - ont conduit l’industrie à développer l’utilisation de matières secondaires et de combustibles alternatifs. Aujourd’hui, avec une part de plus de 50% de combustibles alternatifs dans le mix énergétique, le secteur cimentier est un acteur majeur et précurseur de la récupération et de la valorisation de combustibles de substitution et de matériaux secondaires. Parmi eux, la biomasse-déchet s’adjuge par exemple 30% du fuel-mix des cimenteries belges.
La nouvelle tour qui permettra de capter le CO2 issu de la décarbonatation du calcaire.
Par ailleurs, le granulat calcaire constitue la principale matière première du processus de fabrication du ciment. Or, deux tiers des émissions de CO2 sont dues à la décarbonatation de celui-ci. Parmi les mesures mises en place: la substitution de matières premières par des flux alternatifs ou des sous-produits déjà décarbonatés qui possèdent un apport minéral utile (cendres volantes, laitier de haut fourneau, sables de concassage, béton cellulaire,…).
De même, l’intégration directe de matériaux secondaires déjà décarbonatés en lieu et place du clinker permet de réduire les émissions de CO2 et la consommation d’énergie liées à la fabrication du ciment, sans en modifier les propriétés hydrauliques et mécaniques. Le laitier de haut fourneau et les cendres volantes constituent les matériaux les plus adéquats à cet effet.
1 m3 de béton pèse environ 2,5 t et nécessite 300 à 400 kg de ciment. (© Pluspunt Architectuur - Photo J. Van Hevel)
Le secteur cimentier étudie également la production de nouveaux types de ciments et clinkers issus de procédés de fabrication beaucoup moins énergivores. Par exemple, à basse température ou avec des compositions minéralogiques différentes. Leur déploiement industriel n’est certes pas encore assuré, mais ce n’est qu’une question de temps.
Amélioration de l’efficacité énergétique
Particulièrement gourmand en électricité, le secteur cimentier investit régulièrement afin de doter ses installations des meilleures technologies disponibles et imposées par les autorités. En Belgique, la consommation spécifique est d’environ 110 kWh/tonne de ciment, contre 120 kWh/tonne de ciment en moyenne européenne.
Quant à l’efficacité thermique, elle a permis de réduire les consommations énergétiques des outils industriels de moitié depuis les années 60.
Capture, stockage et utilisation du CO2
Active sur différents fronts, l’industrie cimentière mène aussi d’importantes recherches sur les technologies de capture du CO2 les plus adaptées à son processus industriel. La capture du CO2, son stockage et son utilisation constituent des options prometteuses visant à réduire drastiquement l’empreinte carbone.
A cet égard, le projet pilote de recherche «Leilac» (Low Emissions Intensity Lime and Cement, voir encadré), financé en partie par l’UE, teste le captage de carbone à la cimenterie CBR de Lixhe (Visé).
Bioélectricité
Un autre projet environnemental à l’étude à Lixhe est le Project Bee Green Wallonia (BGW) 20 MW. Il consiste à auto-produire 160 GWh d’électricité verte par an par l’apport de 160.000 tonnes de biomasse. Benoit Gastout, Plant Manager de CBR Lixhe, précise que pas moins de 6 millions de tonnes de ces déchets sont disponibles aux alentours de la cimenterie. La production de cette énergie renouvelable équivaut à 36 éoliennes et permettrait d’économiser 95.000 tonnes de CO2 par an. Un projet qui prend tout son sens au vu du niveau élevé du prix (de la taxation) de l’électricité en Belgique par rapport aux pays limitrophes.
La centrale de bioélectricité prendrait place sur un terrain de 16.000 m2 disponible sur le site de Lixhe et représente un investissement de 90 millions d’euros.
BGW 20 MW n’en est qu’à ses prémices. Si son cheminement (étude d’incidences, permis, études, etc.) suit normalement son cours, il pourrait devenir réalité dans 3 ans.
TOTEM
Début 2018, les trois Régions ont lancé TOTEM, acronyme de «Tool to Optimise the Total Environmental impact of Materials in buildings». Grâce à ce logiciel en ligne, les concepteurs peuvent évaluer objectivement l'impact environnemental de projets de construction complets. Cet impact environnemental total est analysé sur la base des indicateurs CEN connus, complétés par une série d'indicateurs dits CEN+. Il couvre l'ensemble du cycle de vie, depuis la phase de production des matériaux jusqu'au traitement des déchets de démolition. Le résultat est exprimé sous la forme de coût en euros/m² de surface brute au sol. La consommation d'énergie pendant la phase d'utilisation (exigences PEB ou standard passif) est également prise en compte.
Comparaison
A la demande de la fédération des cimentiers, Febelcem, la KUL a passé un projet de maison mitoyenne et d’un immeuble à appartements à la moulinette de TOTEM. Dans le cas de la maison mitoyenne, trois techniques de construction ont été comparées: la brique, le béton et l’ossature bois. La différence de coûts environnementaux entre les trois variantes s'est avérée insignifiante (- de 5%). Le béton occupe la position intermédiaire entre la brique et l’ossature bois. En moyenne, 85% du coût environnemental provient des matériaux et 15% de la consommation d'énergie pendant la phase d'utilisation. Il convient toutefois de noter que la version actuelle de TOTEM ne permet pas ancore de prendre en compte les avantages de l'inertie thermique, chère au béton.
Pour l'immeuble d'appartements, trois variantes ont également été comparées: l’acier, le béton et le CLT (cross laminated timber). En moyenne, les matériaux sont responsables d'environ 90% de l'impact environnemental, tandis que la consommation d'énergie dans la phase d'utilisation représente 10%. Ici, des différences évidentes sont apparues entre les trois variantes, notamment en termes de coûts environnementaux pendant la phase de production. Il s’avère que ces coûts sont presque deux fois moindres pour le béton par rapport à l'acier et près de 30% moins élevés par rapport au CLT.
A noter qu’avec cet outil, la Belgique est un des précurseurs européens dans la promotion de l’application de l’analyse du cycle de vie (ACV) dans le secteur de la construction et dans l’objectivation et la diminution de son impact environnemental.
La cimenterie de CBR (HeidelbergCement) à Lixhe a démarré ses activités dans les années 1950. Elle emploie 180 personnes et produit 1,5 million de tonnes de ciment (12 qualités différentes) par an et 1,4 million de tonnes de clinker. Chaque année, 2,7 millions de tonnes de calcaire sont extraites de la carrière en plus de 1,1 million de tonnes de terres. Lixhe écoule essentiellement sa production de ciment sur le marché domestique (1,4 million de tonnes) et environ 450.000 tonnes de clinker vers les usines du groupe à Gand, Maastricht,… Une partie se fait par la Meuse qui frange le site. Benoit Gastout, Plant Manager de CBR Lixhe, précise le un bilan énergétique du site: ◊ 950.000 tonnes de CO2 émises en 2018 ◊ Taux de substitution avec des combustibles alternatifs: 64,1%, soit 76.900 tonnes de pétrole économisées ◊ Consommation énergétique: 68,5 kWh/t de clinker et 102,8 kWh/t de ciment ◊ Part du clinker dans la production de ciment: 62,8% ◊ Part de l’énergie biomasse: 44% ◊ Consommation électrique annuelle de Lixhe: 176 GWh ◊ 5 millions d’euros investis chaque année dans la durabilité. |
L’usine de Lixhe héberge le projet pilote d’innovation Leilac (Low Emissions Intensity Lime and Cement). Il bénéficie d’un investissement de 20 millions d’euros, dont 12 millions venant de l’UE et le solde des partenaires du projet (HeidelbergCement bien sûr, mais aussi Lhoist, Cembureau, Quantis, Tarmac (groupe Crh), Cemex, l’Imperial College de Londres, Carbon Trust,…). Les études et premières étapes ont débuté en 2016 et il s’étalera sur 5 ans. Une nouvelle tour de 60 m a été construite à cet effet et entrera en fonctionnement ces jours-ci. Elle dispose notamment d’une enceinte en acier supportant des températures allant jusqu’à 900°. En bref, le but est de voir s’il est possible de capter le CO2 issu de la décarbonatation du calcaire, mais aussi d’en étudier l’utilisation ultérieure. A terme et si les tests s’avèrent concluants, l’idée serait d’intégrer cette technologie dans le processus cimentier. Avec une solide réduction des émissions de CO2 à la clef. (www.project-leilac.com) |