Norbord automatise l'étiquetage de 700 palettes par jour
En Belgique, les panneaux OSB sont utilisés dans pratiquement tous les projets de construction ; il est d’ailleurs fort probable qu’ils soient fabriqués au Limbourg. En effet, Norbord Genk fait partie des fabricants les plus importants au monde: ses 125 employés produisent plus de 1.200 m³ de panneaux par jour.
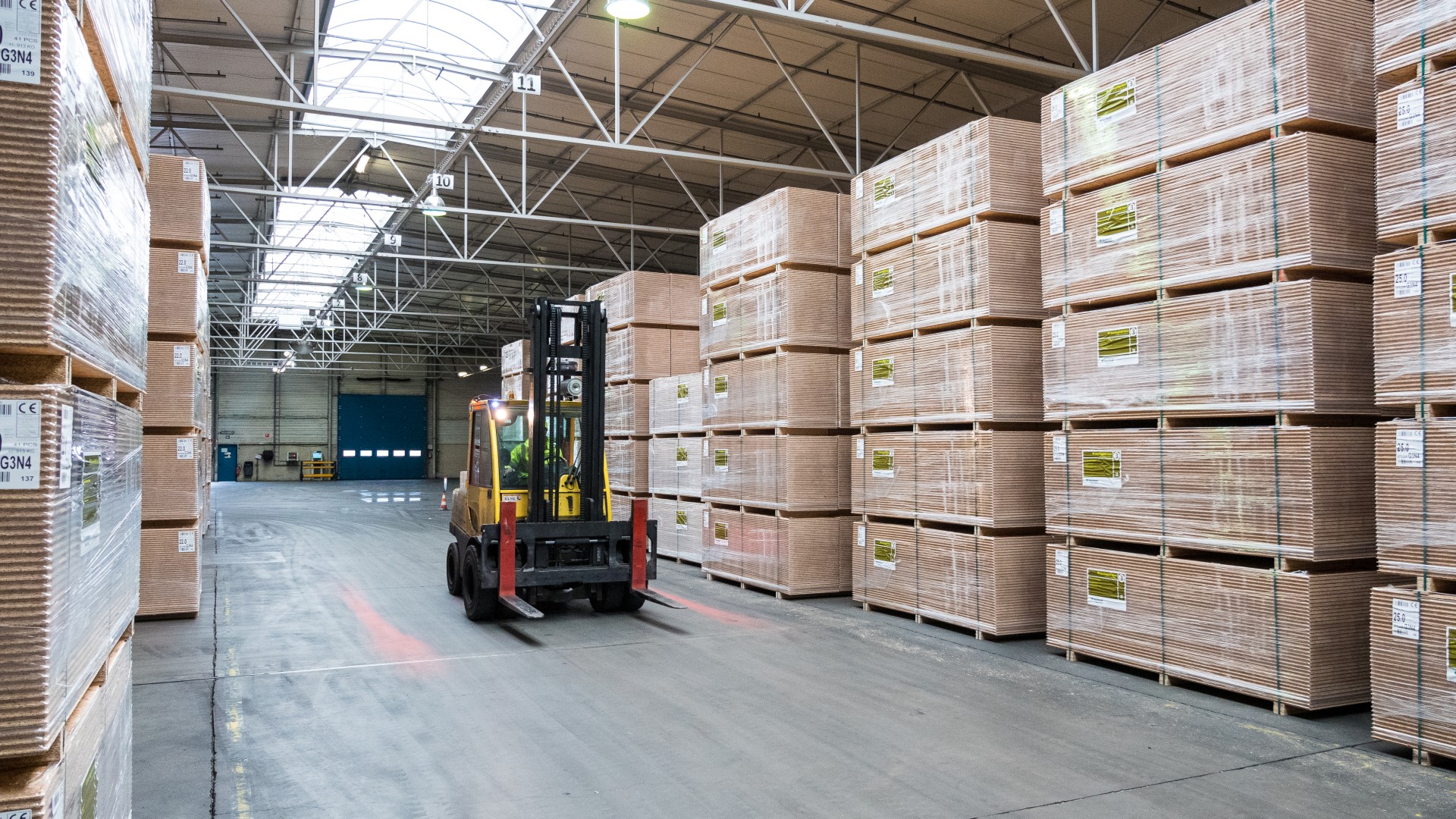
«Dans notre usine, nous broyons des troncs d’arbres pour en faire des panneaux de bois, disponibles dans dix épaisseurs différentes», explique Steven Brouillard, chef du département Finishing End Operations chez Norbord. Les panneaux sont ensuite placés sur des palettes et emballés dans un film de protection, jusqu'à une hauteur standard de 900 mm ou un maximum de 1,5 tonne. Les informations concernant les palettes, les panneaux et leur emplacement dans l’entrepôt sont enregistrées dans le logiciel ERP. Ce dernier imprime ensuite des étiquettes à apposer et à scanner sur les palettes correspondantes.
700 étiquettes produites et scannées
Auparavant, les étiquettes étaient pré-imprimées via le logiciel ERP de Norbord. Les employés devaient descendre de leur chariot élévateur pour les apposer manuellement sur chaque colis après les avoir emballés. «Pendant un moment, nous avons même réaffecté certains de nos employés uniquement à l’application et au scannage de ces étiquettes», confie Steven Brouillard. «Avec un débit de 700 palettes par jour, ce n’était plus possible de continuer ainsi. Sans compter que nous comptions aussi ouvrir une deuxième ligne d’acheminement.»

© Norbord
Pour automatiser le processus, Norbord a opté pour la machine Print and Apply de Zetes. Celle-ci colle les étiquettes, toujours dans la même position, après l'emballage des palettes. Elle scanne ensuite automatiquement les codes-barres indiquant l'emplacement des stocks et les numéros de lots. De cette façon, les palettes sont correctement répertoriées dans le warehouse management software de Norbord. Les chauffeurs saisissent les emplacements des stocks une fois qu’ils commencent leur travail. Après avoir scanné une palette, ils peuvent l'emmener à l'emplacement désigné dans l'entrepôt d’une contenance approximative de 40.000 m³.
Plus de sécurité et moins d'erreurs via l’automatisation
Norbord n’a désormais besoin que d’un seul employé par ligne au lieu de deux. Grâce à l'automatisation, les conducteurs ne doivent plus descendre de leur chariot élévateur pour coller puis scanner les étiquettes sur les palettes. Cela comporte aussi de sérieux avantages en termes de sécurité: les risques de chute sont minimisés maintenant que les employés n’ont plus besoin de descendre et remonter des véhicules à répétition.
«La marge d’erreur est également significativement réduite», commente Stefan Nysen, Systems Developer chez Norbord. «Avant, il arrivait parfois que quelqu’un oublie de scanner une étiquette avant de l’apporter dans l'entrepôt. Cela pouvait aller jusqu’à cinq palettes par jour. Du coup, les emplacements des stocks et les quantités n'étaient plus corrects. Il est impossible de vendre des produits qui ne sont pas enregistrés. Le lendemain, nous devions alors revoir toutes les palettes préparées la veille pour retrouver les "scans oubliés". Cela ne prenait que quelques minutes, mais autant l'éviter si une solution existe…»
Un exemple pour les autres banches
Sans surprise, les opérateurs ont immédiatement adopté le système Print & Apply. D’après Stefan Nysen : «Il s’agissait d’un petit projet pour notre équipe informatique. Cependant nos opérateurs étaient extrêmement enthousiastes de cette nouvelle façon de travailler. Ils ont tout de suite voulu connaître l’appareil, pour le redémarrer en cas de panne lors du travail de nuit notamment. Heureusement, son interface est très simple à utiliser.»

© Norbord
Depuis la mise en place, les autres antennes européennes de Norbord, au Royaume-Uni, s’intéressent à l’application. «Pour le moment, les projets similaires ont été mis en pause à cause de la pandémie. En attendant, nous ne manquons pas de partager notre expérience avec nos confrères», ajoute Stefan Nysen. «Relier des machines industrielles au logiciel ERP est assez complexe. Nous avons pu y parvenir grâce à une bonne coopération entre nos équipes d'ingénierie et informatiques, et aussi grâce à Zetes. La nouvelle machine n’est pas un module isolé rangé au fond de l’entrepôt, elle est entièrement intégrée à notre système d’opérations.»
Une installation rapide
Steven Brouillard conclut : «Nous avions consulté plusieurs fournisseurs pour mettre en place un nouveau dispositif. Avec Zetes, nous avons tout de suite eu l’impression de faire appel à une équipe professionnelle. Ils avaient parfaitement cerné nos besoins. Nous sommes agréablement surpris du temps pris pour finaliser le projet. Nos premiers échanges ont commencé en mars 2019. Six mois plus tard, nos deux machines tournaient à plein régime. Grâce à cette installation rapide, nous avons pu ouvrir une deuxième ligne équipée de cette technologie sans avoir à recruter de nouveaux effectifs. De plus, nous pouvons appeler les collaborateurs de Zetes à tout moment si besoin, c’est très pratique. En y repensant, pourquoi n’avons-nous pas adopté cette solution plus tôt ?»