Une décharge convertie en centre de recyclage
Pour la plupart des gens, les gravats de construction, de démolition et d'excavation ne sont que des déchets non valorisables. Chez William Thompson & Son, on voit les choses différemment.
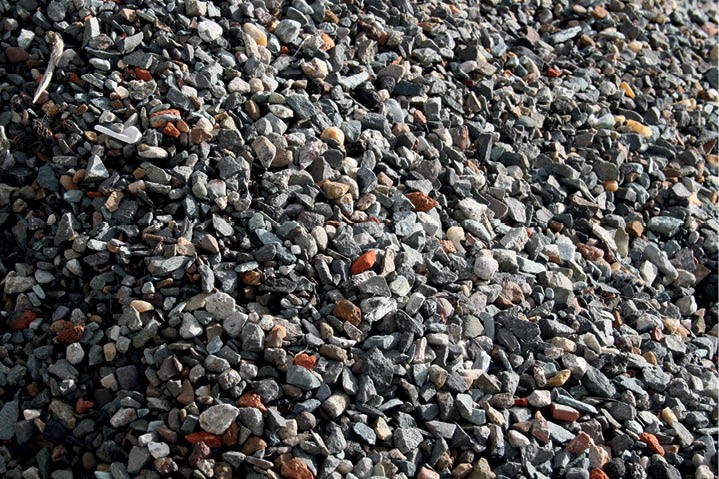
L’entreprise William Thompson & Son, créée en 1946, est basée dans le site de Dumbarton, à Glasgow (Ecosse). L'entreprise qui se consacrait autrefois uniquement à l'exploitation de la carrière, offre désormais toute une gamme de produits pour le secteur de la construction, soit directement, soit via ses filiales. Le groupe a très récemment acquis l’entreprise Thompson’s Recycling & Landfill, spécialisée dans le recyclage des déchets de construction, de démolition et d'excavation grâce à une installation de lavage d'une capacité de 120 tonnes à l'heure fournie par CDE (un important fournisseur d'équipements de lavage pour les carrières, les mines et les opérations de recyclage sur le marché mondial) en janvier 2016.
William Thompson & Son utilise leur installation de recyclage pour le traitement des matériaux provenant de leur décharge et pour celui de matériaux importés. La décharge, installée dans l'ancienne carrière de Rigangower, est utilisée pour la mise au rebut des déchets de construction, de démolition et d'excavation. L'installation de recyclage traite ces déchets et en extrait toute une gamme de produits commercialement valorisables. Environ 80 % des matériaux de la décharge sont aujourd'hui recyclés. Les agrégats de granulométrie inférieure sont utilisés pour la pose des canalisations, les agrégats de granulométrie moyenne pour les systèmes de drainage fermés et ceux de granulométrie supérieure pour les drainages à ciel ouvert. Les graviers de 0 à 4 mm sont très demandés pour la fabrication de parpaings et l'entreprise produit aussi du sable fin de 0 à 2 mm et du sable à béton.
Le plus haut degré de performance comme seule exigence
Après consultation avec l'équipe de CDE, une installation intégrée de recyclage des déchets de construction et de démolition a été conçue qui répond spécifiquement aux besoins particuliers de l'exploitation dans le site de Thompson. L'installation regroupe une unité de criblage primaire R2500, une débourbeuse AggMax 153R, une unité de lavage mobile M2500, un épaississeur AquaCycle, un filtre presse à poutre haute et quatre réservoirs tampons de stockage des boues et de l'eau.
C'est la première fois que l'entreprise fait appel à une installation de traitement par voie humide. «Nos projets antérieurs reposaient tous sur des systèmes de criblage et de concassage à sec, et nous avons effectué beaucoup de recherches sur toutes les options disponibles. Étant donné la complexité de l'équipement et les difficultés associées au traitement de ce type de matériaux, nous savions qu?il allait être essentiel de pouvoir travailler en collaboration directe avec le constructeur», explique Andrew Thompson, directeur de William Thompson & Son.
Une des principales exigences de William Thompson & Son était la fourniture d’un système de criblage primaire évolutif capable de répondre aux besoins du plan d'expansion à long terme. Pour le rendre évolutif, le R2500 a été doté de parois de trémie latérales extensibles permettant une augmentation du volume dans le futur. L'entreprise a également demandé que toutes les passerelles soient interconnectées, de manière à ce que d'un point quelconque, l'opérateur puisse accéder facilement à toutes les parties de l'installation.
Enfin, William Thompson & Son a particulièrement insisté pour que l'installation réponde aux normes de qualité les plus exigeantes. A titre d'exemple: l'entreprise ne s'est pas contentée d'installer des blocs de fondation en béton ordinaires, elle a coulé une dalle de fondation surélevée capable de servir de support à l'installation dans son ensemble. Cet investissement comporte des avantages à long terme dans la mesure où il facilite la tâche de l'opérateur, améliore l'accès et la sécurité, et optimise la disponibilité de l'installation. Idem en ce qui concerne la maintenance. Un contrat de maintenance préventive de deux ans a été conclu avec CDE. Durant cette période, un membre de l'équipe technique CustomerCare de CDE se rendra sur le site une fois par trimestre pour identifier tous les composants d'usure à remplacer et faire le nécessaire pour que l'installation se maintienne au plus haut niveau de performances.
Comme un ballet bien rodé
Concrètement, les matériaux sont véhiculés sur la courte distance qui sépare la pile de la trémie du crible primaire R2500 par une pelleteuse à godets, mais la taille supérieure du caisson d'alimentation permettra à terme le déchargement direct des camions dans l'installation. Le crible primaire permet d'extraire tous les matériaux surdimensionnés de plus de 100 mm. Le R2500 bénéficie de l'incorporation des tout derniers systèmes de criblage haute technologie de la gamme Infinity P2 75R.
Les matériaux de moins de 100 mm sont ensuite véhiculés vers le système de lavage mobile M2500 avec passage sous le séparateur magnétique installé sur le convoyeur d'alimentation (pour une extraction de la fraction ferreuse), puis vers le crible Infinity où ils subissent lavage, classification et déstockage. L'étage supérieur contient tous les matériaux de plus de 40 mm qui sont traités comme des matériaux surdimensionnés. L'étage inférieur contient tous les matériaux de granulométrie comprise entre 4 et 40 mm qui sont ensuite véhiculés par convoyeur vers le débourbeur modulaire Aggmax.
Une fois dans le AggMax, les matériaux argileux sont débourbés et classifiés en trois produits de granulométrie croissante: 4 à 10 mm, 10 à 20 mm et 20 à 40 mm. Les matériaux organiques légers et non valorisables qui flottent à l'arrière du AggMax sont essorés puis déversés dans une benne. Les éléments isolés par la grille d'extraction des déchets et par le crible de classification sont ensuite transférés dans le M2500 où ils sont traités dans la section EvoWash de l'installation qui produit deux types de sable, un sable de 0 à 4 mm et un sable fin de 0 à 1 mm.
Les eaux usées et les vases du cyclone sont transférées dans l'épaississeur AquaCycle où l'addition de floculants permet la séparation de l'eau et des vases. L'eau propre est transférée dans l'Aquastore et les vases pompées dans les réservoirs de boue avant d'être traitées par le filtre presse.
L'installation est équipée de quatre réservoirs en acier d'une capacité de 100 m3 qui ont plusieurs applications. Deux des réservoirs utilisés comme réservoirs de boue alimentent le filtre presse, ce qui permet à l'unité de lavage de tourner au maximum de sa capacité car les réservoirs tampon stockent suffisamment de boue pour empêcher que le filtre presse ne devienne un goulot d'étranglement pour l'ensemble du processus. Un autre réservoir est utilisé comme réservoir principal de recirculation de l'eau. Il stocke toute l'eau récupérée en provenance des autres parties de l'installation et assure l'alimentation des divers systèmes au fur et à mesure des besoins. Le réservoir final est un réservoir tampon de stockage de l'eau qui permet à William Thompson & Son de disposer de la quantité d'eau requise pour répondre aux besoins de l'installation malgré la limitation des volumes d'eau disponibles sur le site.
Le filtre presse à poutre haute est alimenté par les réservoirs tampons. Ce modèle comporte 183 plaques de 1,5 m x 1,5 m. Les plaques se remplissent de boue et elles passent ensuite dans la presse qui produit des gâteaux de filtration secs qui peuvent être déstockés à la pelle. L'utilisation d'un filtre presse permet de recycler 5% d'eau supplémentaire qui sont réinjectés dans l'installation de lavage.