Norbord Genk: l’atout belge de l’Osb
Bien qu’il existe depuis les années 1970, l’Oriented Strand Board, mieux connu sous son acronyme Osb, connaît actuellement un succès grandissant. Utilisé en décoration comme en construction, solide, durable, économique et performant, il a tout pour plaire. Cela tombe bien, le groupe canadien Norbord est le plus grand producteur mondial d'Osb et une de ses filiales européennes les plus importantes est implantée à Genk.
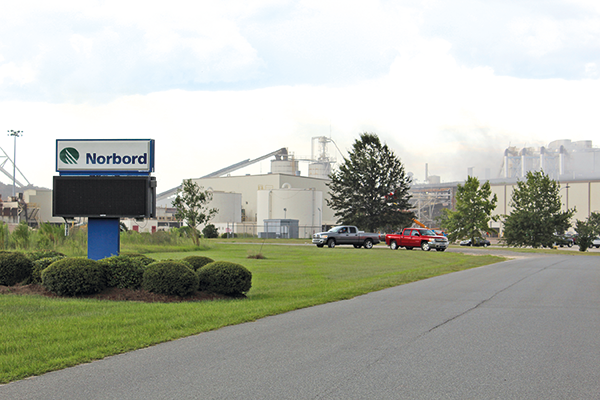
Le Groupe Norbord, basé à Toronto au Canada, est un des principaux producteurs mondiaux de panneaux à base de bois et le plus grand producteur mondial d'Osb (Oriented Strand Board). Outre l'Osb, Norbord produit également des panneaux agglomérés, des panneaux de fibres medium density (Mdf) et des produits apparentés à valeur ajoutée.
Le groupe occupe environ 2.600 collaborateurs (dont le tiers en Europe) sur 17 sites, dans ses usines des Etats-Unis, du Canada et d'Europe. Le siège européen du groupe est établi à Cowie, en Ecosse, mais un autre site européen parmi les plus importants est celui de Genk qui occupe 125 personnes et produit le Sterling Osb-Zero (un panneau Osb sans ajout de formaldéhyde) qui est commercialisé dans toute l'Europe à partir de l’usine limbourgeoise. Les différents panneaux conçus et fabriqués par Norbord connaissent de nombreuses applications: construction de maisons, base pour des armoires et d’autres éléments de la construction intérieure. Le groupe Norbord est coté en Bourse au Toronto Stock Exchange et au New York Stock Exchange.
Un des plus gros fabricants de panneaux Osb d’Europe
Voilà près de 50 ans que Norbord distribue ses produits en Europe. L’entreprise canadienne a fait son entrée sur le marché en 1964, avant même de conclure l'acquisition de ses premiers sites sur le Vieux Continent, en 1988. En l’occurrence, la première usine européenne du groupe a été celle d’Inverness en Ecosse qui produit des panneaux Osb. Elle a également été la première usine d'Osb en Europe à recevoir la certification Fsc qui atteste que le bois qui compose les panneaux provient de forêts gérées durablement.
Deux autres sites verront ensuite le jour au Royaume-Uni: South Moulton en Angleterre, siège de la fabrication de panneaux de particules, de panneaux de revêtement de sol pour lofts et de rayonnages et meubles en kit à monter soi-même. Enfin, le site de Cowie en Ecosse a été le premier au Royaume-Uni à produire des panneaux Mdf et s'est imposé à la tête de l'industrie en matière de développement de produits. C’est également ce site qui a été choisi comme siège européen du groupe.
Dernier venu dans la galaxie Norbord mais loin d’être le moins important, le site de Genk résulte du rachat, en 2004, d’une usine existante de panneaux Osb et de particules. Aujourd’hui, l'usine produit les panneaux Osb dans les limites imposées par sa certification de chaîne de contrôle Fsc. Elle les distribue partout en Europe, avec des marchés importants dans les pays du Benelux, en Scandinavie, Allemagne, France et Royaume-Uni. La production combinée d'Inverness et de Genk fait de Norbord un des plus gros fabricants de panneaux Osb en Europe.
Production à la hausse, nuisances olfactives à la baisse
De fait, depuis son intégration sous la bannière de Norbord, le site de Genk a été transformé en une entreprise fructueuse, malgré les énormes défis auxquels l’économie en général et la région en particulier ont été confrontées. La production a progressivement augmenté depuis la reprise et l’entreprise ne cesse d’investir dans la modernisation de son outil de production. En 2014, un nouveau permis d’environnement a ainsi été demandé pour pouvoir accroître la capacité de production de Norbord Genk de 360.000 à 400.000 m³/an. Suite à l’attribution du permis en automne 2014, Norbord Genk a décidé d’investir 16 millions d’euros sur 3 ans en vue, notamment, de rendre la ligne de production existante plus efficace.
L’année suivante, Norbord Genk annonçait le lancement de son programme visant à passer aux formats de 3 mètres en bois. L'entreprise a investi pour cela 3,6 millions d'euros dans une installation «flaker». L'installation d'alimentation qui amène le bois a donc été partiellement modifiée et renouvelée. Ce fut le cas des bancs de pose pour le délignage, du banc de délignage et du batch feeder. Seuls le magasin des lames et l'écorceur ont été conservés. Ce renouvellement entrait dans le cadre d'un projet d'investissement visant à préparer le site de Genk aux impératifs de demain. Norbord Genk travaillait en effet jusqu'il y a peu avec des panneaux en bois de 2,4 mètres de long. Or, les bois de feuillus et de sapin des forêts locales sont sciés selon la taille standard de 3 mètres. Norbord ne pouvait donc se fournir que de façon limitée sur le marché local. Dans le même temps, l’usine de Genk a significativement augmenté la part de bois de feuillus dans la composition de ses panneaux, laquelle est passée de 6-10% à 15-20%. Avantage collatéral: le fait d'utiliser moins de bois résineux a permis de réduire les dégagements d'odeurs. Enfin, au travers de cet investissement conséquent, Norbord souhaitait envoyer un signal clair aux collaborateurs du site et aux autorités locales en soulignant l’importance de son ancrage régional.
L’atout feuillus
Grâce à l'introduction des feuillus de 3 mètres, la production a augmenté en 2016 et devrait atteindre 385.000 m³ cette année, soit plus très loin du maximum de 400.000 m³ prévus par le lpermis d'environnement. Dans la foulée, Guido Kuypers, directeur de Nordbord Genk, a annoncé que la société poursuivrait son élan en 2017, grâce, entre autres, à une utilisation plus intelligente du stockage externe. «L'objectif de Norbord est de croître en optimalisant le processus existant. C'est le moteur qui nous permet de rester concurrentiels sur un marché où les prix de vente ont chuté de quelque 20% dans les 2 à 3 dernières années», a précisé le manager général.
Une des mesures-phare prises dans le cadre du plan de gestion des nuisances olfactives est l'utilisation d'un pourcentage plus élevé de bois feuillus pauvre en terpène. En comparaison avec le bois de sapin humide, les feuillus, dont le plus utilisé est le bouleau, sont plus secs, ce qui provoque non seulement moins d’odeur, mais permet en outre le passage d'un plus grand volume de bois dans les installations de séchage. Avec pour résultat une augmentation de la capacité. Compte tenu des bons résultats, il est prévu d'augmenter progressivement ce pourcentage dans le futur tout en continuant à garantir la bonne qualité du produit final.
Adie Frydman