Doka Belgium: coffrages ingénieux pour l'A11
L'A11 entre Bruges et Westkapelle, un des fameux missing links (chaînons manquants) identifiés par la Road Federation Belgium, n'est pas une autoroute au sens classique du terme. La morphologie spécifique de certains ouvrages d'art nécessite en effet de recourir à des techniques de coffrages ingénieuses pour former les tabliers des ponts, un viaduc et les parois des tunnels. Des solutions de coffrages spécifiques, tant en termes d'expertise que de technologie et de logistique, ont ainsi été élaborées par le spécialiste Doka Belgium. Il a notamment planché sur des coffrages compatibles avec le système auto-lanceur Berd, une première en Belgique.
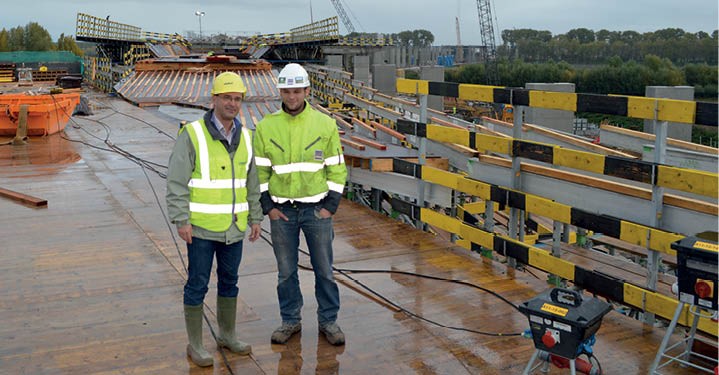
Superstructure de viaduc avec structures métalliques: une première belge
L'élément le plus marquant du chantier de l'A11 est sans conteste le viaduc de 770 m, un des plus longs d'Europe, qui suit le premier échangeur à Bruges. Il se caractérise également par des longueurs différentes entre les piles et par des largeurs différentes entre les traverses en raison de son tracé courbé. Les tabliers sont coulés entre les piles à l'aide d'une structure d'acier à colombages et d'un coffrage intégré. «Ce colombage ' le système auto-lanceur MMS M35I de la société portugaise Berd - comporte un moule de coffrage basé sur notre système Doka Top 50», expliquent Koen Lamers, Managing Director, et Brecht Diependaele, Technical Manager chez Doka Belgium. A mesure que le béton est coulé, la construction est mise sous tension par des câbles afin de compenser les charges de béton et le fléchissement. Doka a donc dû réaliser une étude complexe et approfondie pour tenir compte de ces facteurs, ainsi que des mouvements prévisibles en longueur et en largeur. Des éléments peuvent d'ailleurs être remplacés ou ajustés, tant en longueur qu'en largeur. Le viaduc de l'A11 est le premier ouvrage à être réalisé suivant cette méthode en Belgique.
Par ailleurs, aux croisements du viaduc et de deux lignes de chemin de fer existantes, où le système Berd ne peut pas être mis en 'uvre, un étaiement SL-1 est utilisé comme pont temporaire (quatre phases, allant de 54 à 99 mètres), afin de pouvoir poser par-dessus un coffrage Top 50 pour la superstructure du viaduc, sans gêner le trafic ferroviaire.
L'étaiement SL-1 comme coffrage de tunnel mobile
Pour la construction de deux tunnels au-dessus des voies ferrées de la ligne Bruges-Zeebruges/Blankenberge, une structure SL-1 permet de bétonner les parois du tunnel à partir d'un coffrage-cadre Framax. La dalle de plafond est coulée sur des panneaux Doka 3S0 qui reposent sur la superstructure en SL-1. Le défi consiste ici à assembler la structure en SL-1 durant la mise hors service de nuit, par-dessus les voies et caténaires. La superstructure ne peut pas dépasser une certaine hauteur, afin de ne pas toucher les caténaires ni les pylônes. Après durcissement du béton, le coffrage de tunnel ainsi réalisé sur une longueur de 12,50 m peut être déplacé au-dessus de l'infrastructure ferroviaire du tronçon suivant. Les tunnels sont donc construits sans gêner le trafic ferroviaire.
Parois de tunnel modulables
Une quatrième application du système Doka est illustrée par le coffrage simultané des parois de tunnel avec un côté droit et un côté oblique dans la tranchée d'un kilomètre et demi dans laquelle disparaît l'A11 après avoir enjambé le Tweelingenkanaal et le tunnel emprunté par le trafic venant d'Anvers (direction Bruges), qui tourne à gauche au nouvel échangeur de Westkapelle. «Nous utilisons les panneaux porteurs Top 50 (hauteur maximale de coulée de béton en une fois: 9,8 mètres), ce qui n'est pas une sinécure, surtout à hauteur de l'échangeur», explique Koen Lamers. «Du fait que le tunnel tourne, le sol est en pente et l'intérieur des parois du tunnel est incliné selon un angle qui varie jusqu'à 15°. C'est non seulement la hauteur des parois qui varie (dans le sens longitudinal), mais aussi leur épaisseur à la base (dans le sens transversal). Ces écarts sont assez complexes à compenser par un coffrage. Un peu plus loin en direction de Bruges, en revanche, nous avons une inclinaison constante de 5° et un sol plus plat, ce qui est évidemment plus simple. A la demande du consortium d'entreprises, le coffrage a été conçu de manière à ce que, après bétonnage des parois les plus hautes, les panneaux puissent être réutilisés pour couler les parois de hauteur plus réduite en les raccourcissant systématiquement.» En d'autres termes, Doka a une fois de plus engagé toute son expertise et son inventivité technique dans ce projet. Le timing, le système complet proposé par Doka, la quantité énorme de coffrages à fournir (la plus importante en Belgique pour le moment) ainsi que la possibilité de travailler sans nuire au trafic ferroviaire ont, eux aussi, fait la différence en faveur de l'entreprise de Ternat.
L'A11 en chiffres
Ce n'est pas tous les jours qu'on construit une nouvelle autoroute dans notre pays. Loin de là. Néanmoins, entre la N31 à Bruges et la N49 à Westkapelle, se déroule, dans tous les sens du terme, la nouvelle A11 qui totalisera 12 km et environ 70 ouvrages d'art. Les travaux, menés en DBFM, ont débuté en mars 2014 et devraient être achevés à l'automne 2017. L'A11 facilitera la liaison entre le port de Zeebrugge et l'intérieur des terres. En séparant le trafic portuaire du trafic local, on améliore la sécurité et on favorise l'essor économique du port.
'Si on considère l'ampleur, la cadence de travail et les solutions techniques de l'A11, il s'agit véritablement d'un projet de Champions League.'
Parallèlement, la nouvelle A11 réduira la charge et le trafic touristique sur les routes locales entre Bruges, Dudzele, Lissewege et Westkapelle. De nouvelles liaisons locales pour voitures et vélos rendront la circulation dans les polders plus agréable.
Quoi qu'il en soit, le contrat de ce chantier est mené à bien par Via A11 dont les actionnaires sont DG Infra+, Inframan, Jan De Nul, Van Laere, Aswebo, Aclagro et Franki Construct, ainsi que Via-Invest, une association entre l'Awv (l'agence flamande de la route et de la circulation) et la Pmv (ParticipetieMaatschappij Vlaanderen). Hormis les capitaux des actionnaires, la société est également financée par une obligation (project bond). Pour la conception, la construction et l'entretien de l'A11, Via A11 fait appel aux entreprises Jan De Nul, Van Laere, Franki Construct, Aswebo et Aclagro. Au début des travaux, le coût total du projet était estimé près de 700 millions d'euros.
Le tracé de l'A11 peut, grosso modo, être divisé en un viaduc implanté dans une zone relativement urbanisée et devant croiser des cours d'eau et des chemins de fer, d'une part, et un tracé avec tunnels dans un paysage de polders, d'autre part. Le viaduc possède de grandes portées et un tablier mince afin de laisser les perspectives ouvertes. Il est également scindé en deux parties parallèles afin de ne pas priver les prairies qu'il surplombe de lumière naturelle.
Quant aux tunnels, ils auront une chaussée en béton armé continu tandis que les ponts et les autres voiries auront un revêtement en asphalte peu bruyant.
Les travaux de l'A11 représentent 2,46 millions de m3 de déblais et 3,6 millions de m3 de remblais. Ils nécessiteront 330.000 m3 de béton (fourni par la centrale Interbeton des environs), 33.000 tonnes d'acier, 320.000 tonnes d'asphalte, 2.700 contrôles qualité, 4.096 documents d'étude et 3.800 pieux de fondation. Ils entraîneront dans leur sillage la réalisation de 15 km de nouvelles pistes cyclables, 28 km de nouveaux égouts, 3 échangeurs et 9 ecopassages. Seuls les tunnels, les échangeurs et les bretelles d'accès et de sortie seront éclairés. Pas moins de 350 ouvriers s'activent en moyenne chaque jour sur ce vaste chantier ainsi que 50 employés.
'La morphologie spécifique de certains ouvrages d'art nécessite de recourir à des techniques de coffrages ingénieuses pour former les tabliers des ponts, un viaduc et les parois des tunnels.'
Comme le résume Koen Van Regenmortel de l'entreprise Jan De Nul, «si on considère l'ampleur, la cadence de travail et les solutions techniques de l'A11, il s'agit véritablement d'un projet de Champions League. Nous réalisons par exemple une section en 8 à 10 jours et, dès le départ, nous avons veillé à réduire le nombre de joints au minimum. Il en résulte un plus grand confort de conduite, moins d'entretien et moins de bruit».
F.G.